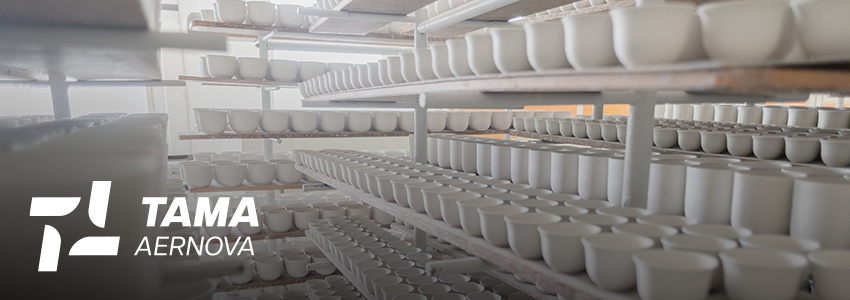
Industria cerámica: reducir el impacto y generar valor como objetivo para el futuro próximo
La cerámica es un activo fundamental para la manufactura europea, teniendo en cuenta la herencia y el volumen de negocios generado por los distritos históricos (especialmente italianos y españoles), productores de bienes destinados a diferentes aplicaciones que van desde los objetos de diseño a los funcionales, hasta la realización de componentes de precisión. En su simplicidad, la cerámica es un material precioso, especialmente por sus propiedades mecánicas y físicas - dureza, impermeabilidad, resistencia, baja conductividad térmica y eléctrica, refractariedad - que la hacen extraordinariamente versátil en sus posibilidades de uso y flexible en los procesos que desde la materia prima conducen al producto terminado. Basta pensar en la variedad de realizaciones posibles: desde los azulejos hasta los sanitarios, desde la vajilla hasta el arte decorativo, desde los materiales refractarios hasta los ladrillos.
A nivel químico, se trata de un compuesto de sustancias naturales ubicuas y en sí mismas inofensivas que, en el ámbito de los procesos de transformación y elaboración industrial, plantean problemas críticos que los operadores deben afrontar para cumplir con la normativa de referencia y garantizar la salubridad del entorno de trabajo. El tratamiento de materiales inertes como el vidrio y la cerámicaes, de hecho, uno de los sectores industriales con mayor impacto ambiental; esto depende de procesos extremadamente energéticos que también afectan a la combustión a temperaturas especialmente altas y tienden a generar cantidades significativas de residuos, incluidos residuos sólidos, partículas finas y contaminantes del aire.
Industria cerámica: las mejores tecnologías filtrantes para la gestión de los contaminantes de proceso
El ciclo de producción de la cerámica comienza con la selección y preparación de la materia cerámica, que se tritura y tamiza para limpiar las impurezas y eliminar los contaminantes y las granulometrías más gruesas. A continuación, se procede a lamezcla de los polvos y al modelado del producto manufacturado, que precedeal secado al aire y a la cocción en hornos especiales hasta una temperatura de 2000°. La última fase se refiere en cambio a los acabados, como el esmaltado con revestimientos de tipo vítreo más o menos cubrientes, que tienen esencialmente el objetivo de mejorar las características originales de la materia y proteger la pieza del desgaste; en algunos casos, la aplicación de esmaltes y otros agentes químicos puede determinar la necesidad de cocciones adicionales a temperaturas más bajas. Cada uno de estos pasos implica la intervención de sustancias y reacciones químicas que deben prestarse atención de manera específica.
En los últimos veinte años, las nuevas tecnologías de producción y la adopción de una planta depuradora de última generación han permitido a la industria cerámica italiana reducir las emisiones contaminantes a la atmósfera en más del 90 %. Según un estudio reciente, la concentración de los principales contaminantes emitidos por las instalaciones de baldosas cerámicas (partículas, flúor y plomo) ha disminuido progresivamente y es inferior a los límites indicados en las MTD (Best Available Techniques).
El contaminante principal siguen siendo las partículas (PM10), seguidas de otros derivados de la combustión como los óxidos de nitrógeno (NOx), los óxidos de azufre (SOx), el monóxido de carbono (CO), el dióxido de carbono (CO2)y los compuestos orgánicos volátiles (COV) derivados de una combustión incompleta y de la consiguiente volatilización de la materia orgánica asociada a la materia prima. En el caso de la cerámica avanzada o técnica, producida con fabricación aditiva - AM, Addictive Manufacturing, es decir, mediante la adición de sustancias químicas (boruro, carburo de silicio, óxidos de aluminio, estaño, circonio) capaces de actuar y potenciar selectivamente algunas cualidades originarias de la materia prima, a la lista se añaden otros contaminantes, por ejemplo, los ácidos fluorhídrico (HF) y clorhídrico (HCL).
Las tecnologías para el sector industrial cerámico, diseñadas, producidas y distribuidas por TAMA AERNOVA en el mercado nacional y extranjero, se refieren principalmente a los filtros de mangas Pulco Air con tecnología pulse jet para mantener limpia la superficie filtrante a través de chorros automatizados de aire comprimido y cumplen con los criterios de las Mejores Técnicas disponibles en materia de filtración industrial del aire. Además del sistema de captación, los materiales de construcción de los distintos componentes de la planta - aceros industriales inoxidables y anticorrosión- y las precauciones en el diseño del producto, benefician el rendimiento y el ahorro energético de la planta. Los filtros de mangas Pulco Air interceptan los movimientos aeráulicos, eliminan el polvo más fino y conservan las impurezas más gruesas en la tolva de recogida (también personalizada). Si es necesario, los filtros de mangas Pulco Air pueden equiparse con sistemas de inertización, como el dosificador de cal, para tratar previamente las partículas no quemadas y los contaminantes más agresivos, garantizando el cumplimiento de la normativa vigente.
Las soluciones diseñadas por TAMA AERNOVA garantizan una gestión metódica y cuidadosa de las criticidades derivadas de todo el ciclo de elaboración de la cerámica, en lo que respecta a la reducción de polvos y humos y a la reducción de las emisiones a la atmósfera y al entorno de trabajo, para favorecer un respeto cada vez mayor del medioambiente y de las personas.
Póngase en contacto con nosotros rellenando el formulario